- Tapering Between Centers The Mechanical
- Tapering Between Centers The Mechanic Certification
- Tapering Between Centers The Mechanic Technician
Pitch reviewed several studies and their protocols, as well as the “watch and wait” recommendation by Phillip 1 2015 and the gradual taper recommended by both Connolly 2 2012 and Richeri 3 2013. 4 2018 meta-analysis of 18 studies published between 2002 and 2018 was reviewed revealing rTMS maintenance may enhance the.
- Mold taper is an important control parameter in the continuous casting of steel billets. Properly tapered mold walls compensate for shrinkage of the solidifying strand to maintain good contact and heat transfer between the mold wall and shell surface without exerting extra force on the hot and weak shell. The amount of taper needed.
- Motor Vehicle Mechanic's Textbook, Fifth Edition is a textbook on the maintenance and repair of motor vehicles that balances theory and practice. Topics covered range from engine principles and components to maintenance of the lubrication, cooling, and fuel systems.
- Asked on December 20, 2019 by Srujan Mechanic A uniformly tapering vessel is filled to the top with a liquid of density 9 0 0 k g m − 3. The force that acts on the base of the vessel due to the liquid is ( g = 1 0 m s − 2 ).
To turn a workpiece between centers, support it between the dead center (tailstock center) and the live center in the spindle nose.
A lathe dog (Figure I-178) clamped to the workpiece is driven by a drive, or dog, plate (Figure I-179)mounted on the spindle nose. Machining with a single-point tool can be done anywhere on the workpiece except near or at the location of the lathe dog. Turning between centers has disadvantages. A workpiece cannot be cut off with a parting tool while being supported between centers, as this will bind and break the parting tool and ruin the workpiece. For drilling, boring, or machining the end of a long shaft, a steady rest is normally Figure I-178 Lathe dog (Micro-Mark). used to support the work, but these operations cannot be done when the shaft is supported only by centers. The advantages of turning between centers are many. A shaft between centers can be turned end for end to continue machining without eccentricity if the live center runs true (Figure I-180). This is why shafts to be subsequently finish ground between centers must be machined between centers on a lathe. If a partially threaded part is removed from between centers for checking and everything is left the same on the lathe, the part can be returned to the lathe and the threading resumed where it was left off.
Lathe Centers The center for the headstock spindle is sometimes referred to as a live center because it rotates, in contrast with a nonrotating
dead center in the tailstock spindle. The live center rotates, and the dead center does not. However, innovations such as ball bearing tailstock centers that do rotate make this terminology confusing if not obsolete. Such ball bearing centers are commonly called live centers even though they are used in a tailstock spindle and not the headstock. To avoid difficulties in terminology in this text, the center in the headstock is referred to as a live center, and a nonrotating tailstock center as a dead center. To avoid confusion, a ball bearing center will not be referred to as a live center even though that is common terminology in the shop.
Tapering Between Centers The Mechanical
The center for the headstock spindle is usually not hardened, because its point frequently needs machining to keep it true. Thoroughly clean the inside of the spindle with a soft cloth and wipe off the live center. If the center is too small for the lathe spindle taper, use a tapered bushing that fits the lathe. Seat the bushing firmly in the taper (Figure I-181) and install the center (Figure I-182). Set up a dial indicator on the end of the center (Figure I-183) to check for runout. If there is runout, remove the center by using a knockout bar through the spindle. Be sure to catch the center with one hand. Check the outside of the center for nicks or burrs. These can be removed with a file. Check the inside of the spindle taper with your finger for nicks or grit. If nicks are found, do not use a file but check with your instructor. After removing nicks, if the center still runs out more than the acceptable tolerances (usually .0001 to.0005 in.), a light cut by tool or grinding can be taken with the compound set at 30 degrees.
A chuck center is often machined from a short piece of soft steel mounted in a chuck (Figure I-184). It is then left in place, and the workpiece is mounted between it and the tailstock center.
A lathe dog with the bent tail against a chuck The lathe dog on the workpiece is driven by one of the chuck jaws.Jaw is used to drive the workpiece. This procedure sometimes saves time on large lathes where changing from the chuck to a drive plate is cumbersome,and the amount of work to be done between centers is small.The nonrotating tailstock (dead) center (Figure I-185) is hardened to withstand machining pressures and friction.Clean inside the taper and on the center before installing. Ball bearing antifriction centers are often used in the tailstocks, as they will withstand high-speed turning without the overheating problems of dead centers. Needle bearing and ball bearing
centers are used extensively in machine shops and manufacturing operations.
Dead centers are virtually obsolete but have the advantage of greater rigidity. Rolling pipe centers are used for turning tubular material (Figure I-186). Ball bearing centers are shown in Figures I-187 and I-188.To set up a workpiece that has been previously center
drilled, slip a lathe dog on one end with the bent tail toward the drive plate. Do not tighten the dog yet. Put antifriction Center carbide tip
Figure I-189 Antifriction compound put in the center hole before setting the workpiece between centers. This step is not necessary when using an antifriction ball bearing center. compound into the center hole toward the tailstock and then place the workpiece between centers (Figure I-189). The tailstock spindle should not extend out too far, as the machine will lose rigidity, and chatter or vibration may result. Set the dog in place and avoid any binding of the bent tail (FigureI-190). Tighten the dog and then adjust the tailstock so there is no end play but so the bent tail of the dog moves freely in its slot. Tighten the tailstock binding lever. The heat of machining will expand the workpiece and cause the dead center to heat from friction. If overheated, the center may be ruined and may even be welded into your workpiece. Periodically, or at
the end of each heavy cut, check the adjustment of the centers and reset if necessary.
Incoming search terms:
Tapering Between Centers The Mechanic Certification
- turning between centres
- shaft mounted between centers
- turning a long stainless shaft between centers
- holding a work beetween the chuck
- how to set work piece between a lathe
- chuck for turning between centers
- setting of turning work piece between a lathe
- setting turning work piece between a lathe
- what is turning between centres in a lathe machine
- turn between center drive center

Related posts:

owned by the Joe Martin Foundation
Not all machine tools are big
Joe Martin loves machine tools of all sizes, but he has a special love for machines at the small end of the size scale. Upon leaving the radio control industry in the 1970's he began as an importer for small lathes from Australia that were to be sold by Sears under the Craftsman name. He also marketed the tools himself under the Sherline name and eventually began producing them in the United States in 1974, having purchased the rights to do so. Expanding the tool and accessory line over the years has given him an appreciation for what these early manufacturers had to deal with in the design, production and marketing of small tools. A few years ago Joe began purchasing small tools as he found them available at shows or auctions. Several have since been donated by other patrons who appreciate small tools and want share them with others. This is just the basis of a good tool collection. The foundation plans to continue to add to this collection as interesting machines become available.
Seeing the tools in person is an interesting walk through history, from the first simple hand-cranked watchmaker lathes to the electronically speed controlled, laser engraved machines made today. Since not many people can visit the collection in person, we will document each machine here on the Internet Craftsmanship Museum as well for the world to view. As more machines are added to the collection, they will be added here too.
Tapering Between Centers The Mechanic Technician
The Miniature Machine Tool Collection
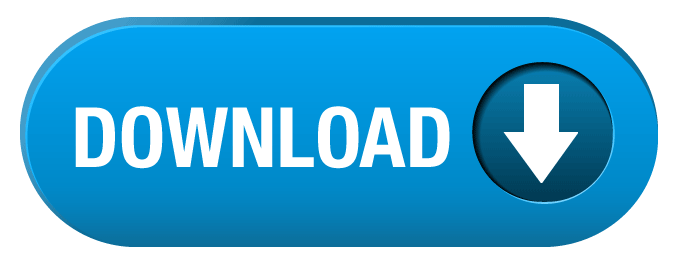